This new release of FLOW-3D is packed with useful features and capabilities across the spectrum of industrial applications. The following summary highlights the key new benefits offered in Version 9.4.
Contact us to find out how you can purchase or lease the new version of FLOW-3D.
New CFD Modeling Capabilities
Multi-Sediment Scour and Bedload Transport Model
The sediment scour model has been extended to allow the simulation of multiple species of sediment. Among other things, this will allow users to model sands, silts and fine gravel in a single simulation. The addition also includes a bed-load transport model which describes the transport of heavier debris by the currents along the top of the packed bed.
Scour Potential Model
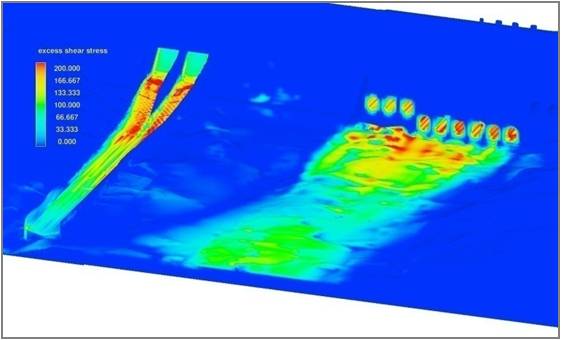
Excess shear stress on the riverbed.
In conjunction with the changes to the sediment scour model, a new scour potential model has been added to FLOW-3D. This model is a simplified version of the sediment scour model in that, rather than computing the transport of sediment, the model evaluates the excess shear stress (that is, the shear stress above which scouring may occur) along solid surfaces. The scour potential model allows users to evaluate the likelihood of scour without incurring the computational expense of using the full scour model.
For more detail on both models, refer to the Development Note in the Spring 2009 Newsletter.
Core Gas Generation and Transport
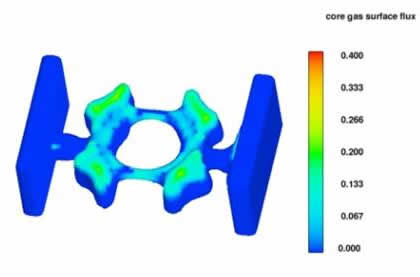
Gas mass flux at the core surface.
A new core gas model has been introduced in version 9.4. This model describes the generation of gas in sand cores during the pouring and cooling of metal. The gas comes from the decomposition of the sand binder due to the heat coming from the metal. The model is based on first principles and aims at capturing in detail the heat transfer between metal and mold, binder pyrolysis and the flow of gas within the core, and its venting at the core’s external surfaces.
The core gas model can be used together with filling and solidification simulations. The model predicts the gas pressure and velocities, and evaluates the mass flux of gas at core prints, at the open surfaces and, most importantly, into the metal.
Read more about the Core Gas model in Flow Science Technical Note #84.
Non-Linear Stokes Wave
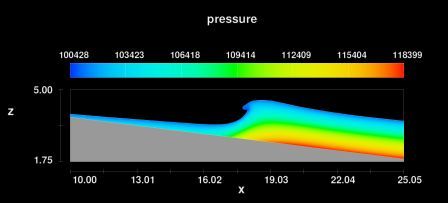
FLOW-3D v9.4 produces a realistic simulation of a 5th-order Stokes wave
FLOW-3D’s linear surface wave boundary condition has been complemented with the addition of a new fifth-order non-linear Stokes wave model. The model allows users to introduce periodic surface waves at higher amplitude and steeper profile than can be allowed for the linear wave model.
For more detail on this new model, refer to the Development Note in the Summer 2009 Newsletter or to Flow Science Technical Note #78.
Temperature-Dependent Materials
Thermo-physical properties of some fluids and solids vary significantly with temperature. Taking into account this behavior is important for obtaining accurate numerical solutions. Version 9.4 of FLOW-3D allows users to define these properties as a function of temperature in a tabular form. Almost all properties of fluid and geometry components, including the fluid/solid heat transfer coefficients, can now be defined as a function of temperature.
For more detail on this addition, refer to the Development Note in the Summer 2009 Newsletter.
Additions to the General Moving Objects Model
The General Moving Objects model, introduced in version 9.0 of FLOW-3D, is again the subject of more extensions and improvements, as customers stretch the model and seek greater functionalities. The most important addition for version 9.4 is the ability to model objects attached to one another by springs or ropes.
Springs & Ropes Capability
FLOW-3D simulation of an
offshore oil
platform tethered to the seabed.
Objects with coupled motion can be tethered by spring or ropes to other moving or stationary objects or to arbitrary fixed points in space. Several types of springs can be modeled such as expansion, compression and torsion springs. This will give FLOW-3D users an even greater breadth of applications that they can model. For example, spring forces and torques can be applied to valves and other moving mechanical parts in numerical simulations. In ocean engineering, users can study the stability of Floating Production, Storage, and Offloading (FPSO) systems. Motions of floating wave power generation systems, mooring of ship and marine measurement equipment and boat towing can also be simulated.
For more detail on this new capability, refer to the Development Note in the Fall 2008 Newsletter.
Control forces with application points
In version 9.4, users will be able to define up to three control forces and the points of their application on a moving component, making it easier to represent real life situations. Previously, all forces had to be converted to a single force and torque acting at mass center.
Buoyant stability
The user can request the evaluation of the buoyancy center on a submerged moving object. The buoyancy center is computed as the geometric center of the displaced fluid volume assuming the free surface is relatively flat and facing the positive z-direction.